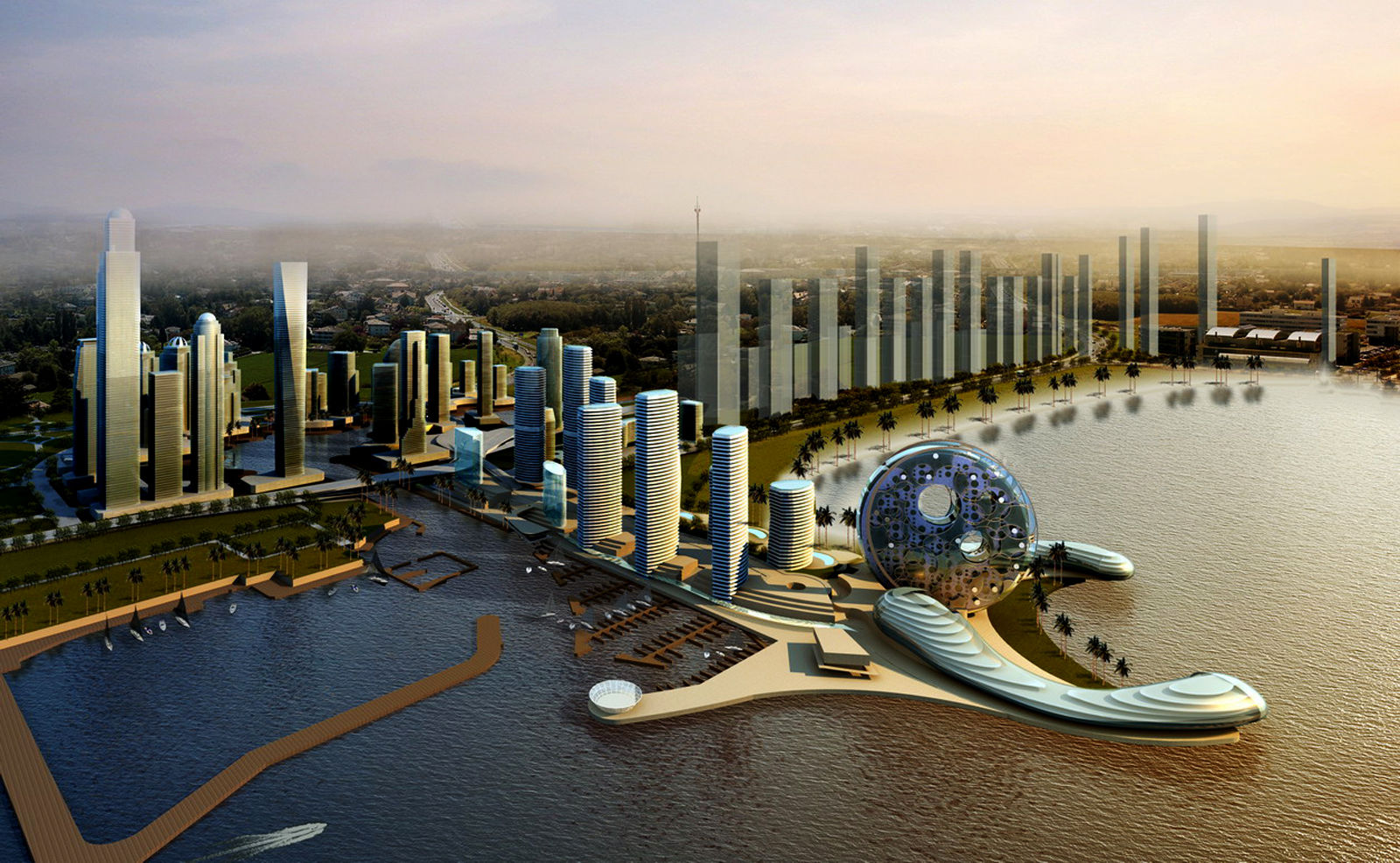
Futuristic Buildings
FB | Today's Technology is Solving Yesterday's Problems

What IS Prefabrication?
Benefits



Social
Benefit
Environmental Benefit
Economic
Benefit
1) Shorter Construction Duration
Factory-produced building components are built earlier in factories. Meanwhile, parallel actitivies can occur on-site. Significant time savings in assembly of various components on-site. Minimal disruption due to external variables such as weather as well.
2) Controlled Quality
More elaborate and better organization and inspection processes can used for prefabricated modules in the factory as opposed to at the construction site. Computer-assisted models allow the completed building to be visualised, enabling prediction of most factors that could affect the construction process.
3) Reducing Labour & Upgrading Employment
Fewer skilled workers needed on-site for assembly operations. Shortage of on-site labour is a huge problem affecting tradtional construction approaches, especially in remote locales. With aging populations and higher labour cost, semi-skilled workers can be hired to perform the same well-defined task at a lower cost, freeing the precious pool of skilled workers for more complex operations.
4) Productivity and Economies of Scale
Factory production allows for efficient mass production, allowing for quick response to market conditions. Mechnical process of factory production contributes to productivity gains. Increasing use of manufactured components from outside the traditional construction sector, increasing commercial competition. Bulk orders from a factory brings significant benefits as compared to one-off building orders
4) Other Economic Benefits
Faster construction times allow housing projects to be released into the market earlier, reduing financing costs. Factory produced components also have a longer shelf life, reduing maintenance & repair expenses.
1) Reduced Material & Construction Waste
Factory produced components are built with accuate cutting, aligning, screwing, nailing, painting and handling due to automated processes. This drastically reduces amount of material wastage. With less on-site plastering or timber works, on-site construction waste plummets.
2) Reduced On-Site Pollution
Less on-site activities and factory-finished interior works, there is less noise, dust and litter produced, resulting in better air quality for the households as compared to traditional construction methods.
3) Increased Use of Recycled Materials
Referred to as "Cradle to Cradle", a lean construction principle allows for solutions of reusing and recycling components and materials in building construction. This is as opposed to the traditional "Cradle to Grave" construction process.
4) Better Energy Efficiency
With less energy used in transporation and on-site works, energy consumption is reduced greatly. Most components and modules are pre-fabricated with economies of scale, reduing the energy per unit usage.
1) Reduced Accidents and Illnesses
With less exposure to noisy, dirty, polluted construction sites, construction workers face less accidents or suffer less illnesses. Factory production allows for improved safety and environmental efficiencies, and can be aided by compuer controlled autonomous mechanical operations for integrating, joining and assembling, reducing the worker's exposure to hazards.
2) Improved Job Conditions and Wage Levels
Most construction processes actually occuring away from the building site, in an arguably safer and more stable factory environment. With task specific semi-skilled and skilled labourer, their earning capacity stands to increase together with the productivity increases.
Prefabrication
A manufacturing process, generaly taking piace at a specialised facility in which various materials are joined to form a component part of a final installation
Preassembly
A process by which various materials, prefabricated components and/or equipment are joined together at a remote location for subsequent installation as a sub-unit
Module
A major section of a plant resultingfrom a series of remote assemblyoperations and may include many portions. It is isusually the largest transportable unit or component of a facility
Off- Site Prefabrication
The practice or preassembly or fabrication of components off-site and on-site at a location rather than the final installation location. Increasingly common to adopt the term 'IOP' which refers to 'industrialization, offsite manufacture and prefabrication